Challan – Inventory & Job Work
Management System

About the Client
Our client operates in the job work industry, managing complex subcontracting processes and inventory flows. They faced challenges in tracking raw materials, monitoring job progress, and maintaining transparency in subcontractor transactions.
To address these issues, they sought an advanced system that could streamline inventory management, improve workflow automation, and ensure accurate material utilization. The goal was to enhance efficiency, reduce wastage, and establish a seamless job work tracking mechanism.
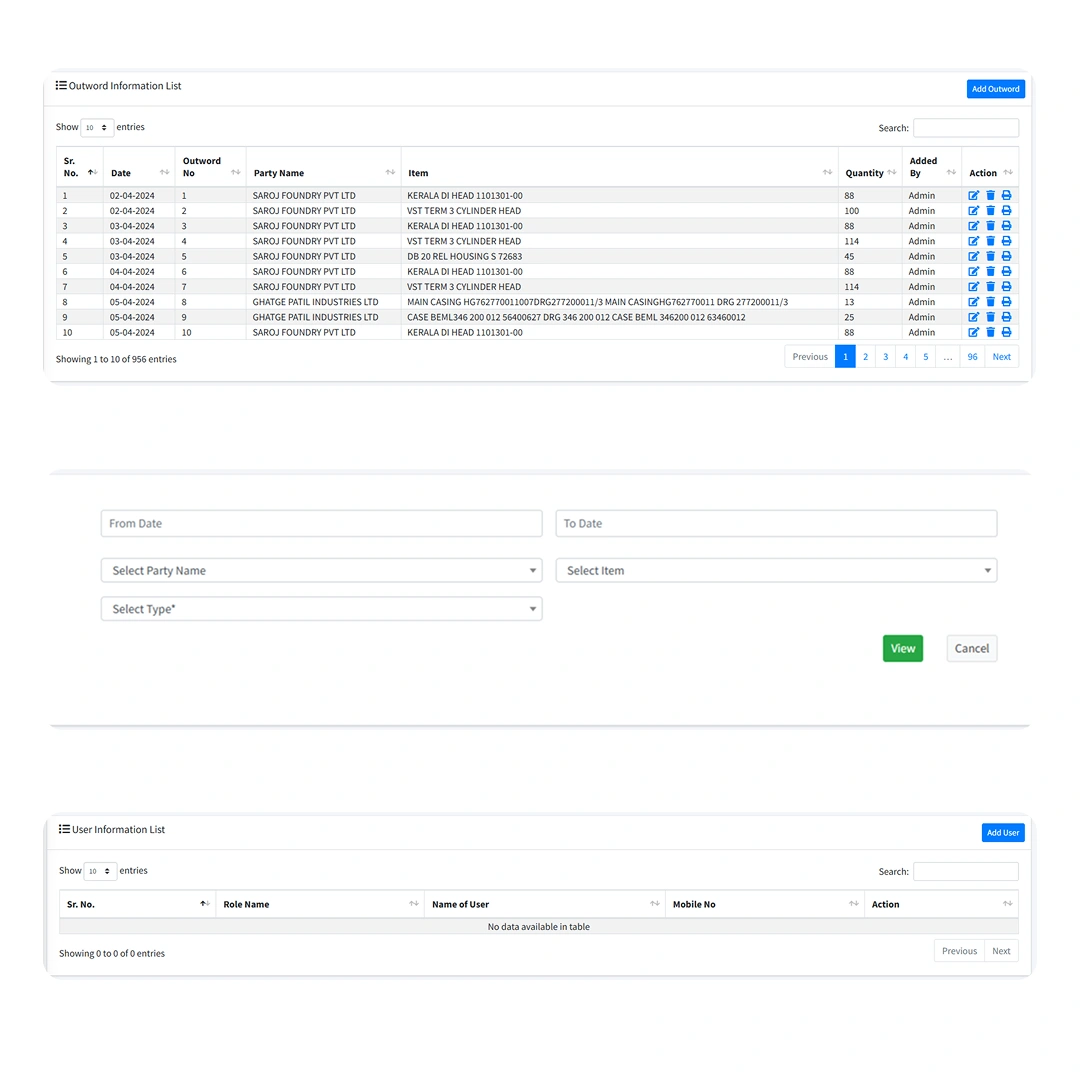
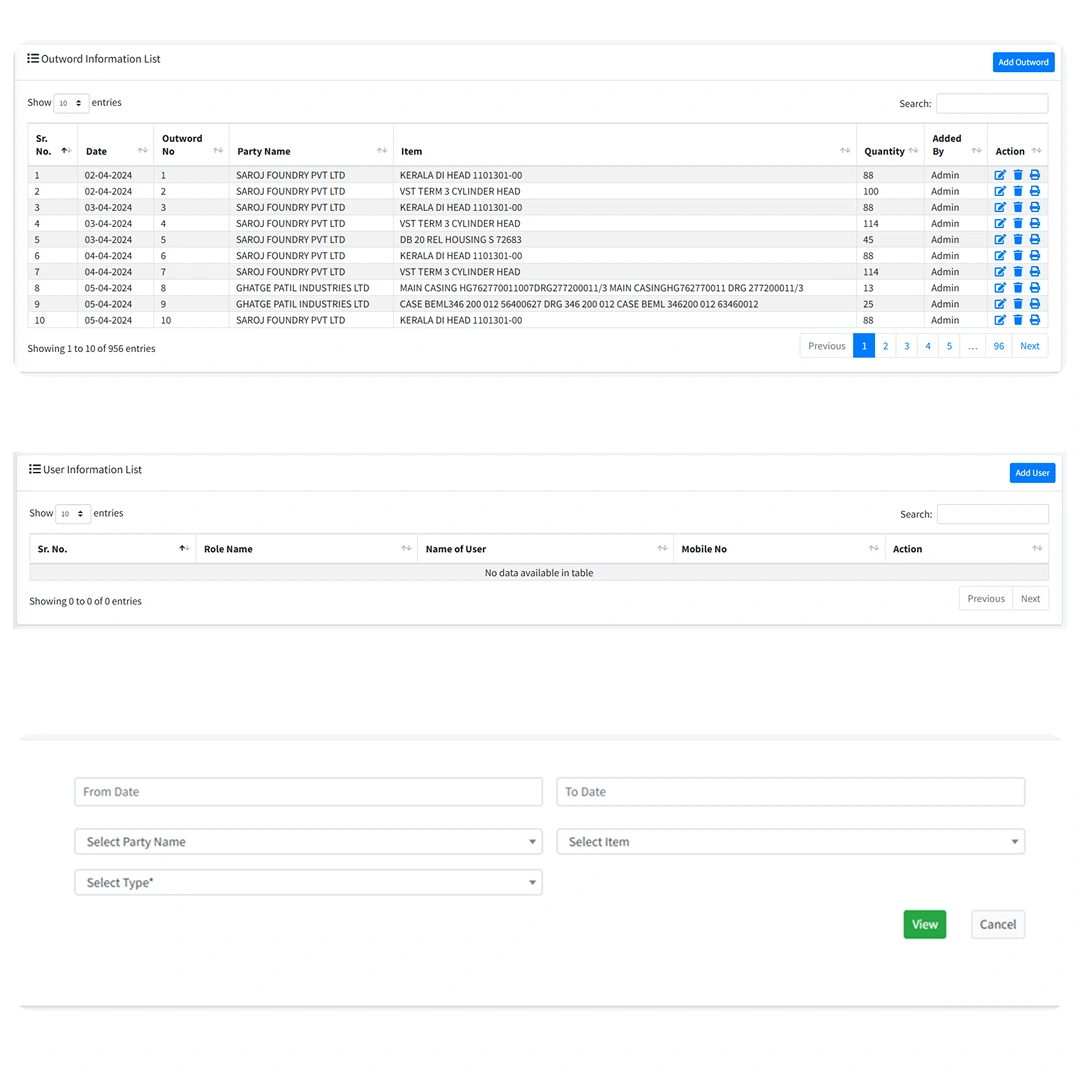
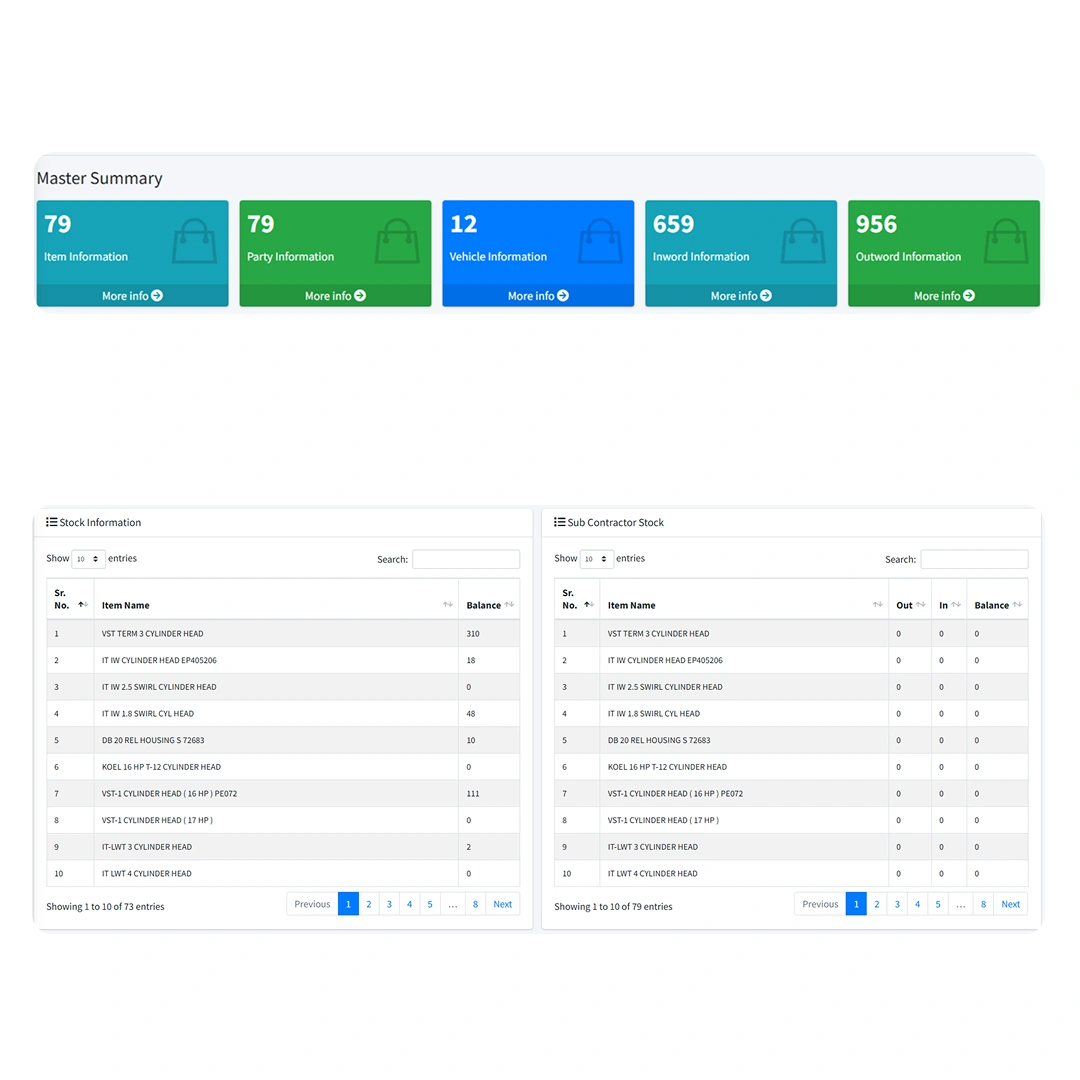
Challenges Faced by Challan


Manual Inventory Tracking
Before implementation, tracking inventory across multiple subcontractors was done manually, leading to discrepancies, delays, and inefficiencies. Lack of real-time visibility resulted in stock mismanagement and material shortages.

Subcontractor Accountability
Ensuring transparency in job work processes was challenging, as there was limited control over materials issued and received. Without a structured system, monitoring subcontractor performance and tracking work progress was cumbersome.

FIFO Implementation Issues
Maintaining a proper First-In-First-Out (FIFO) stock utilization method was difficult without automation. Materials were often used out of order, leading to increased wastage and inefficiencies in production planning.
Proposition Offered

Automated Inventory Tracking
Implemented a real-time inventory management system to track material movements accurately, reducing errors and ensuring stock optimization.

Enhanced Subcontractor Monitoring
Developed a structured job work tracking system to improve subcontractor accountability, ensuring transparency in issued and received materials.

FIFO-Based Stock Management
Integrated a FIFO (First-In-First-Out) mechanism to streamline material usage, minimizing wastage and improving production efficiency.

Workflow Automation
Digitized job work processes with automated tracking, reporting, and alerts, enabling seamless operations and reducing manual efforts.
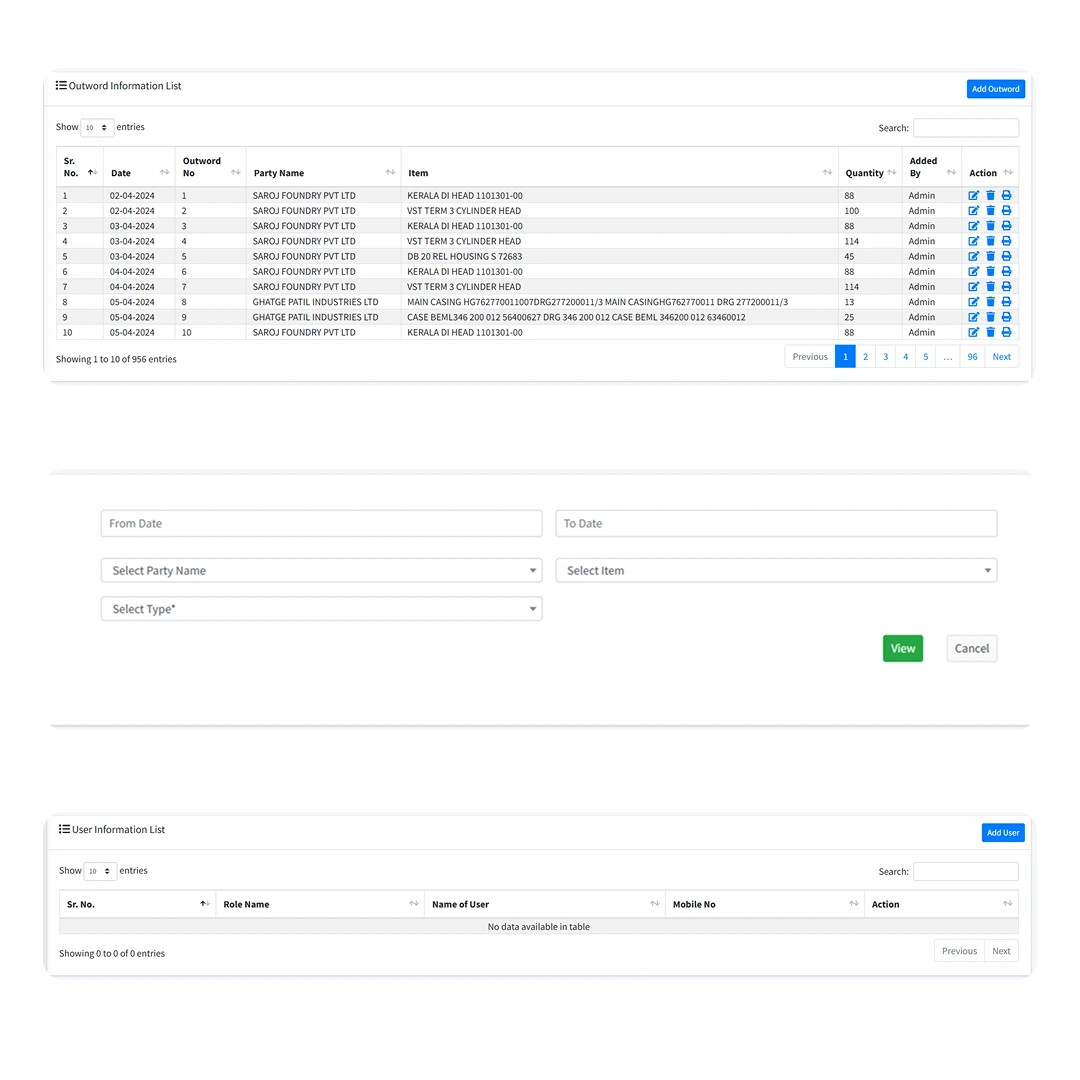
Key Technologies & Platforms

Front end
React.js
Angular
Tailwind CSS
Bootstrap
Services Used
AWS
Stripe / Razorpay / PayPal
Twilio / SendGrid
Google Maps API
Back end
Node.js
MySQL / PostgreSQL
Our Approach
To address the client’s challenges, we began by analyzing their existing inventory and job work processes. Our team conducted an in-depth assessment to identify inefficiencies in manual tracking, subcontractor accountability, and stock utilization. Based on these insights, we designed a customized Challan – Inventory & Job Work Management System that seamlessly integrates with their workflow, ensuring real-time inventory visibility and control.
We implemented automation tools to track inventory movement, enforce FIFO stock management, and enhance subcontractor monitoring. Our system provided instant updates on materials issued and received, reducing errors and improving decision-making. Additionally, we incorporated workflow automation features, including reporting and alerts, to streamline operations and enhance overall efficiency in the job work process.

Persistent Development

On-time Delivery

Outstanding Results
Outcomes
With the implementation of Challan – Inventory & Job Work Management System, the client achieved accurate inventory tracking, reduced material wastage, and improved subcontractor accountability. The FIFO-based stock management ensured optimal resource utilization, while real-time monitoring enhanced transparency in job work processes. Overall, the system streamlined operations, increased efficiency, and minimized manual efforts.
- Accurate Inventory Tracking Real-time monitoring reduced errors and ensured precise stock management across multiple locations.
- Improved FIFO Implementation Automated FIFO-based stock utilization minimized wastage and optimized material flow.
- Enhanced Subcontractor Accountability Transparent tracking of materials issued and received improved reliability and performance evaluation.
- Reduced Manual Efforts Automation eliminated the need for manual record-keeping, saving time and reducing human errors.
- Seamless Job Work Monitoring End-to-end tracking of job work processes improved visibility and operational control.
- Optimized Material Utilization Efficient stock management reduced excess inventory and prevented shortages.
- Faster Decision-Making Real-time data insights enabled quick and informed business decisions.
- Error-Free Documentation Automated reports and logs ensured accurate records for audits and compliance.
- Increased Operational Efficiency Streamlined workflows reduced delays, improving overall production timelines.
- Cost Savings Reduction in material wastage and manual labor contributed to significant cost savings.
- Scalability for Future Growth The system provided a flexible framework to accommodate business expansion.
- Improved Customer Satisfaction Faster and more efficient job work processes enhanced client service and reliability.